Bearing and shaft repair
- scrivyscriv4
- Jan 1, 2021
- 2 min read
The power feed lead screw is a standard left hand 1/2” acme thread, mated to a brass acme nut attached to the carriage with a small bolt. Inside the unsealed lower gearbox is a compact transmission, driven by a bevel gear tower shaft mated to the spindle in the upper, sealed, gearbox.

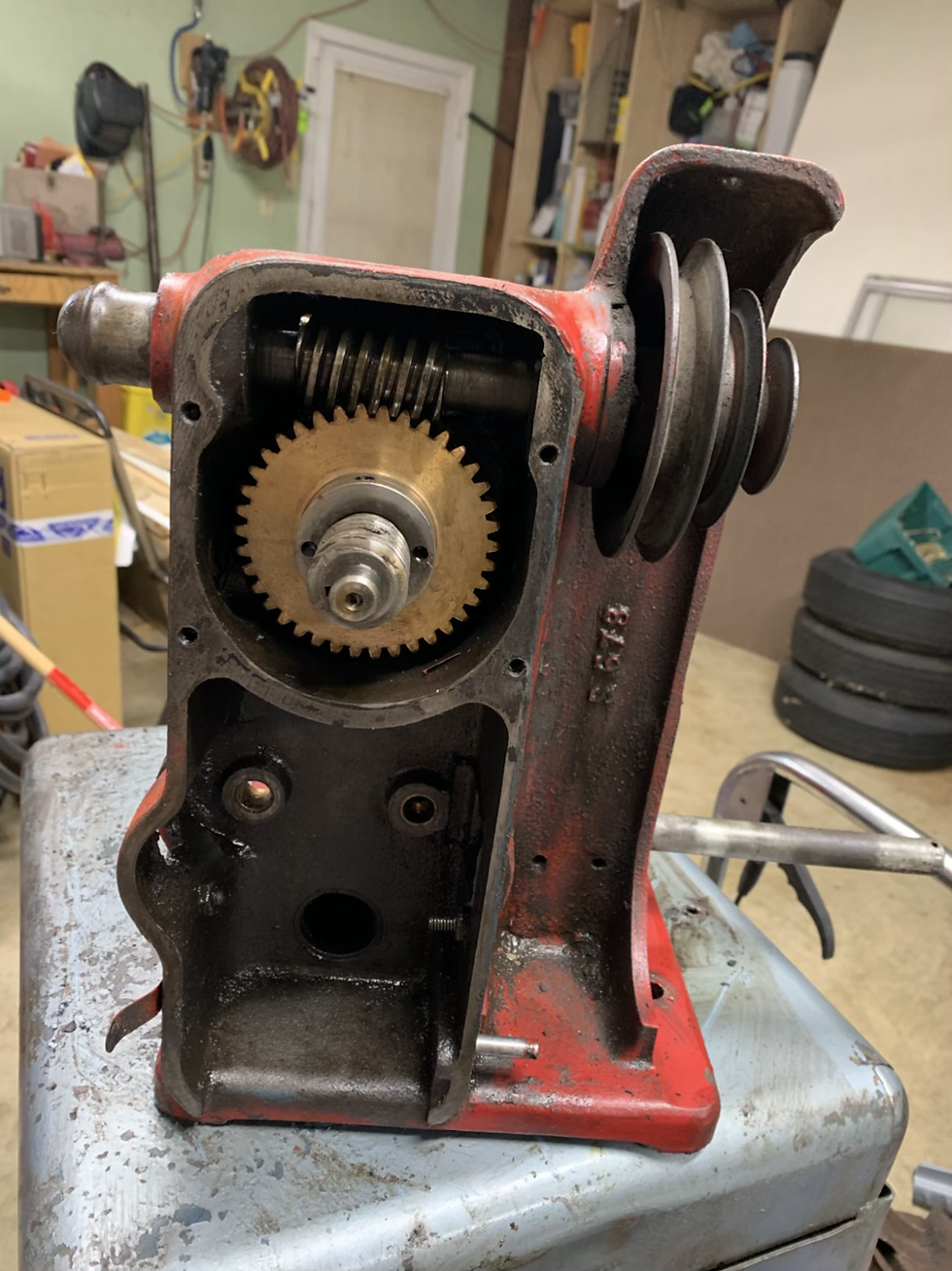

So as you can see in the photos, the main shaft spindle has an auxiliary worm gear at the end, which mates with the tower shaft gear in the lower photo.
The tower shaft is housed in the rear casting, which also provides bearing support for the carriage leadscrew and gearbox idler shaft. It does not contain a bearing for the spindle; although the casting is machined for the spindle to ride in a boss, there is no bushing present. The spindle load is taken up at both ends with a tapered roller bearing.
The upper gearbox contains the drive gears - a worm screw shaft driven by a three speed pulley, and the brass worm wheel. Note the brass gear: when selecting gear oil, you must not use an oil rated API GL-5, unless it is specifically indicated to be compatible with yellow metals. GL-5 has historically contained enough phosphorous to corrode yellow (brass) metals over time.

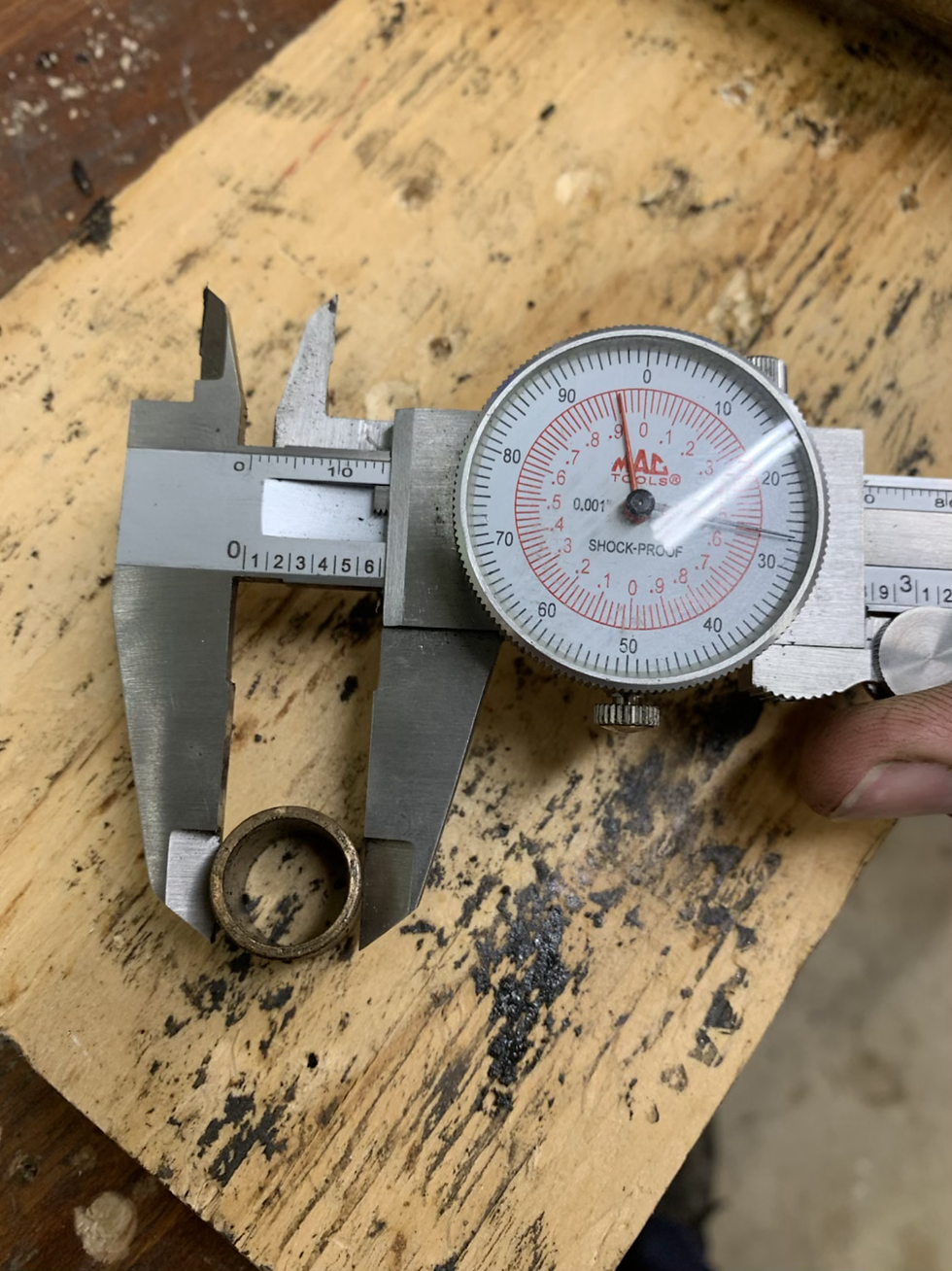
All four shaft bearings are plain oilite bearings with no thrust surface. They are 1/2” ID x 5/8” OD x 5/8” long, and there is room in the castings and on the shafts to install a longer bearing for more shaft support. The reason this transmission had a hard time going in gear was evident when inspecting the bearings... when the bearings wear, the two shafts do not stay parallel, which allows the selector casting to hit a gear on the idler shaft.

The lead screw shaft has a flat machined an inch from the end, for the handwheel set screw. Unfortunately because of the flat, I was unable to straighten the shaft - the tip simply shattered at the edge of the flat, where all the stress concentrated. Although I could have made a new shaft from 1/2” acme threaded rod, I would have needed to machine two key slots for the gear set and that is a lot more setup and work. I decided to weld on a section of 5/8” dia 1018 carbon steel rod and turn it down to 1/2”.

I tig welded the new rod in place but couldn’t avoid a few low spots due to the base metal pooling in to the weld area, so I will add some metal epoxy in to fill the low spots. Normally I wouldn’t worry about them, but the bearing rides the shaft here and low spots would end up causing accelerated bearing wear.
Commentaires